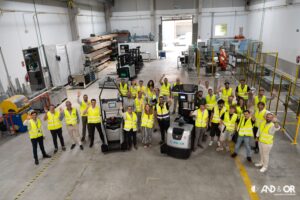
On June 24 and 25, we opened the doors of our facilities in Palomares (Seville) to celebrate a new edition of our Open Days alongside clients and collaborators.
More than 30 professionals from over 20 companies across various sectors joined us to get an up-close look at our automation solutions, share experiences, and exchange ideas about the current and future challenges of the industry.
CONFERENCES THAT CONNECT INDUSTRY AND THE FUTURE
During the event, attendees had the opportunity to attend presentations delivered by leading brands in automation, logistics, and industrial digitalization. These sessions addressed the current challenges of the sector and the technological solutions already transforming intralogistics in real environments. We would like to thank BITO, SICK, and SIEMENS for making the event even more insightful.
Topics covered:
- How automation and connectivity are building the intralogistics of tomorrow, today
The AND & OR team provided a clear overview of the current situation in many industrial plants, where processes are fragmented and have a low level of digitalization. Based on this diagnosis, we presented how it is possible to advance towards a more efficient, connected, and automated model.To achieve this, we introduced the AND & OR ecosystem of solutions that enables this transition progressively, realistically, and tailored to each industry’s needs: real-time data monitoring systems, intralogistics solutions through mobile robots (AMRs), and intelligent warehouses with fleet managers.
- How to choose the optimal storage system for palletized goods
A review of different types of storage systems and the key factors for making efficient decisions based on load type, available space, and required automation level. - Challenges and solutions in the implementation of AMRs and AGVs in industrial environments
A session focused on critical factors for integrating autonomous mobile vehicles, including practical cases and technical recommendations. - Tracking and traceability on-site with RFID: operational efficiency and use cases
How RFID solutions are optimizing process traceability on-site, improving operational efficiency and real-time visibility of workflows.
And the best part: after the presentations, attendees were able to see in real operation some of the solutions presented — including AMRs and AGVs in action — during the visit to our facilities. This was a unique opportunity to experience firsthand how automation translates into efficiency, coordination, and tangible results on the plant floor.
The true value of these Open Days lies not only in the technology showcased but also in the connections and learnings we have built together. We are very grateful for your participation and commitment.
Would you like to discover how our solutions can transform your business?
Write to us, and we’ll be happy to assist you with anything you need.
Leave A Comment