Technical assistance is one of the main concerns of customers. An immediate response can mean a significant reduction in production costs for manufacturers.
The entry of industry 4.0 has led to the development of remote technical assistance, immediately and regardless of the distance to which the client is.
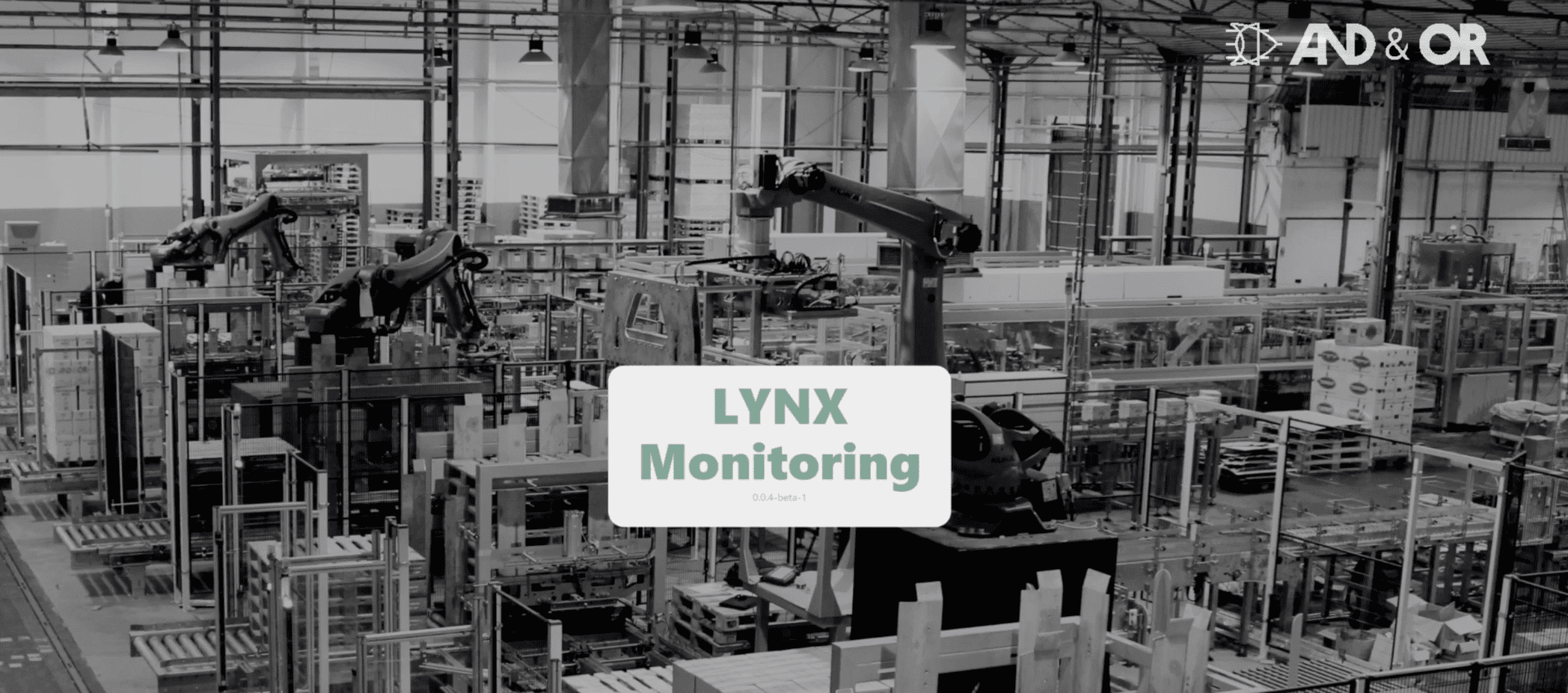
AND&OR and Industry 4.0
In the current context of digitization of the industry, AND&OR offers the AND&OR INDUSTRY 4.0 digital platform, allowing remote assistance in the packaging industry as well as data extraction directly from the production machines, its subsequent processing and conversion into data of interest to improve production efficiency.
AND&OR, as an engineering company and machinery manufacturer with more than 36 years of experience, has proven capacity for the design and programming, commissioning, installation and support of INDUSTRY 4.0 solutions, to achieve a factory connected with the highest standards. of security.
The AND&OR INDUSTRY 4.0 platform is a technological solution that integrates different services through an IoT platform and digital tools. The platform is open to customization according to customer requirements, new variables and KPIs, new reports and notifications.
In turn, it allows connection with ERP and MES customer management systems.
In this video AND&OR shows us four digital solutions.
Remote assistance in industry 4.0: key in the collaboration between suppliers and customers
With the changes introduced by Industry 4.0, the client benefits from greater control of production and ensures efficiency at all times.
Ensuring efficiency, precision and speed will be essential aspects that must be met to satisfy the needs and requirements of customers.
With Industry 4.0, machinery manufacturers such as AND&OR maintain a continuous interaction with customers. Virtual technical assistance can resolve any issue remotely, without impediments of distance and incompatible schedules. Statistical data with AND&OR monitoring allow processes to be improved, resulting in greater satisfaction and long-term relationship with customers. Industry 4.0 reduces operating and maintenance costs.
The Industry 4.0 technologies developed at AND&OR allow the supplier-client relationship to be closer, fostering collaboration to achieve product and process innovation.
Leave A Comment