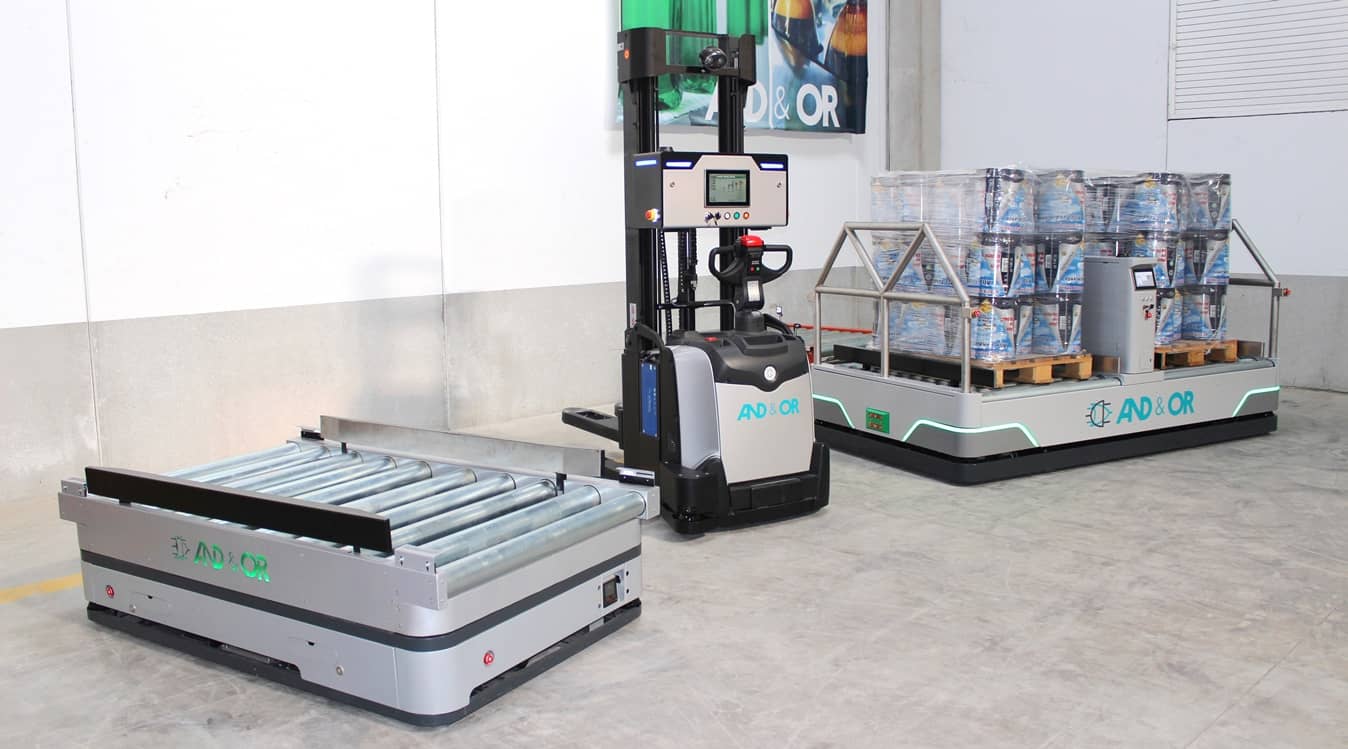
In the previously published article “AMR: la nueva generación de vehículos autónomos” se explicaban las diferencias entre AGV y AMR, así como las prestaciones diferenciales del AMR.
Work options on AMR smart vehicles
In this article, we want to expose the 2 possible work options for AMRs, considering whether it is better for these intelligent vehicles to make use of all their capabilities, and allow them to avoid the obstacles that arise while executing their different routes, or, on the contrary, it is preferable to have more control over their movements and that they work with established virtual paths.
Figure 1. AMR virtual paths
The answer depends on the needs of the application in question.
For example, on some occasions, if the vehicle is small, and its operating space is crowded by many people, avoiding the obstacle can be an efficient approach. This is the case of autonomous cleaning or disinfection robots so used during this Covid pandemic.
On the other hand, it is important to highlight that for most industrial applications, using a virtual fixed route to manage AMR missions is the best option, since production plants require precise recurring movements to achieve efficient processes. .
The main reasons behind this choice are listed below:
- Moving around an obstacle reduces overall efficiency, and can lead to straying from the optimal route.
-
- In complex and space-constrained environments (such as industrial production plants), there is often no room to move around obstacles.
- In large vehicles, personnel may not be sure how the vehicle will avoid the obstacle, causing stressful situations and increasing the perception of risk among operators (even when the risk is minimal due to laser safety systems).
- Traffic management is much more efficient with the virtual route tracking option. If AMRs choose their own routes to avoid obstacles, fleet traffic problems are virtually impossible to avoid.
- If the AMRs are free to overcome obstacles, the plant personnel may be less careful in respecting the free spaces of the routes for the movement of vehicles, tending to worsen the lay-outs for efficient merchandise management.
As a conclusion, in most of the cases for applications in production plants, controlling the route of the AMRs through virtual routes (stopping and waiting when they encounter an obstacle), is the most efficient approach, and it provokes a greater sensation of control. and security in the organization of production.
VIDEO:
Leave A Comment